Overview
SMIW Co searching and developing a lot of solutions in order to seek ways and means for achieving sustainability in all human activities and industries.
Currently SMIW Co. is in the final stages of development modern advanced oxidation technology, the process optimized to provide efficient and reliable destruction of sulfide mercaptans and COD in spent caustic and other liquid waste treatment applications.
Supplied in a batch reactor working under ambient pressure and temperature minimizes the cost and safe operation. Clear water will be produced and the by product is iron oxide as a comprehensive economical recycle. a chemical treatment technology to treat and safely dispose one of the most challenging waste streams at the Refineries and petrochemical industries which is spent caustic waste.
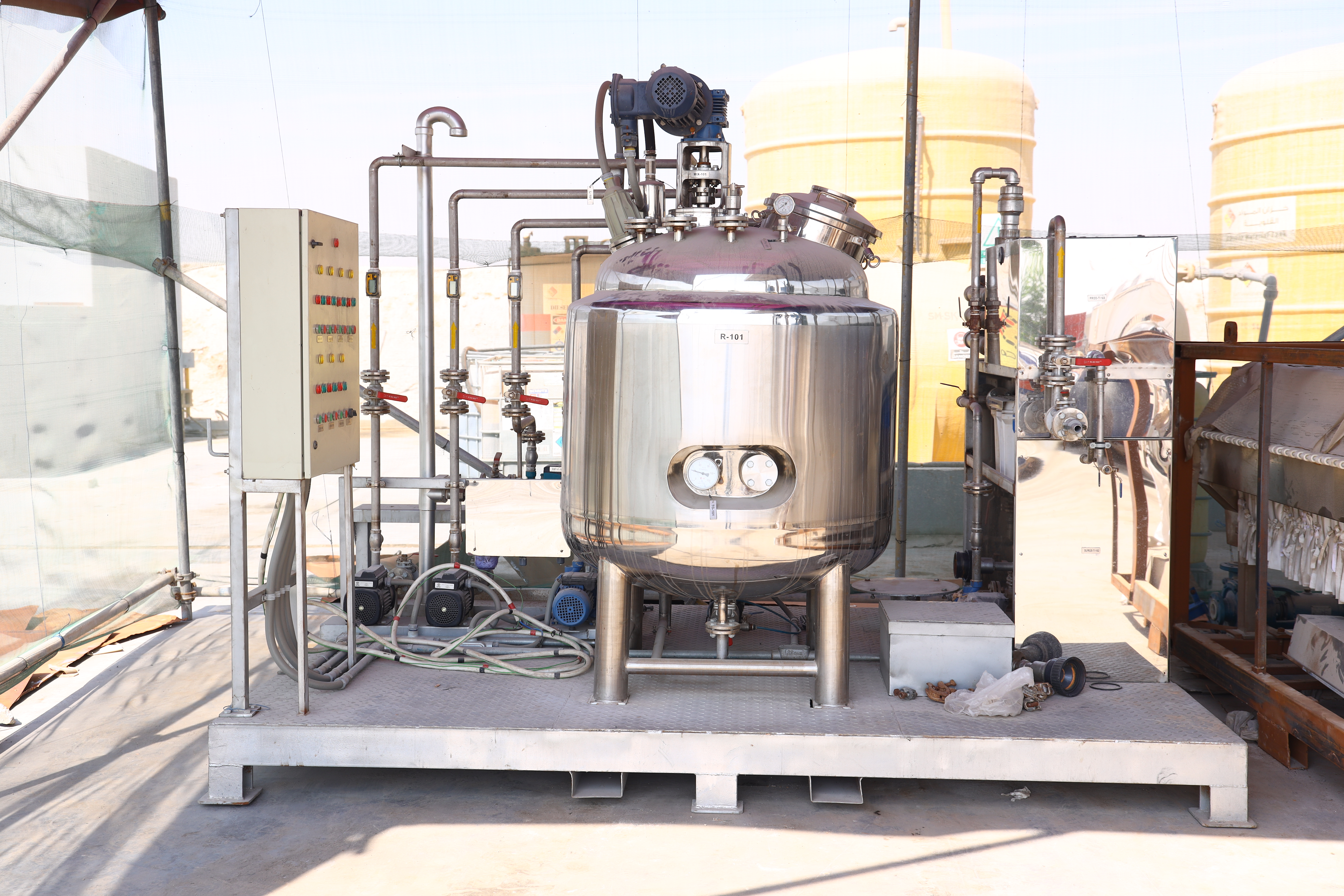
Field of Application
SMIW Tech is an advanced oxidation process using hydrogen peroxide (H2O2) as the oxidant and is targeted at the treatment of sulfidic spent caustic and other liquid waste treatment applications. Spent caustic is a noxious and toxic waste product generated by the oil and gas industry as a by-product. With a purely sulfidic spent caustic feed, SMIW Tech offers COD reduction in excess of (98.5-99)% and sulfide reduction to less than 0.5 ppm thus allowing treated effluent to pass through filter press to remove the sludge. The sludge has 30% iron Oxide can be produced once the sludge pass through the thermal unit. Then the effluent will be clear water.
The Process
SMIW Tech is an oxidation process with a capacity up to 5 m3 per day that treats liquid streams with chemical oxygen demand (COD) up to 100,000 mg/l. Waste liquid is treated in a jacketed stirrer reactor and a temperature can be started with ambient and using hydrogen peroxide as the oxidant. The reactor residence time is typically 18-20 minutes which is optimal for ensuring maximum destruction of COD. The sulfur-containing compounds, as they occur in spent caustic for example, are oxidized and form sulfate and water Organic compounds can be either fully oxidized to carbon dioxide or partially oxidized to low toxicity compounds suitable for biological treatment. Toxic and odorous compounds are neutralized.
The Technology
The waste liquid and acidic catalyst are pumped to the reactor then H2O2 is injected and then exothermic reaction will be raised up to 92 C and the emission will pass through scrubber to make sure no toxic gases get out the system
- Easy mobilization, Easy Feeding
- Working under ambient temperature and pressure
- Low power consumption
- Complete dosing system
- Can treat COD up to 100,000 mg/l
- Batch reactor with capacity of 0.5 m3/45 min
- Safe operation
- H2O2 used as the oxidant
- Low maintenance cost
Design Summary
Capacity | up to 5 m3/day |
---|
COD Feed Concentration | 1,000-30,000 mg/l | 30,000-65,000 mg/l |
---|---|---|
Hydrogen Peroxide Consumption (35 wt%) | 5% of the feed | 10 % of the feed |
Sludge percentage | 28-35% (by product- Iron Oxides) |
---|---|
Electrical Consumption | 15-20 kW |
Air Consumption | Minimal for H2O2 injection |
plant dimensions (L x W x H) | 3 m x 2 m x 2.5 m |
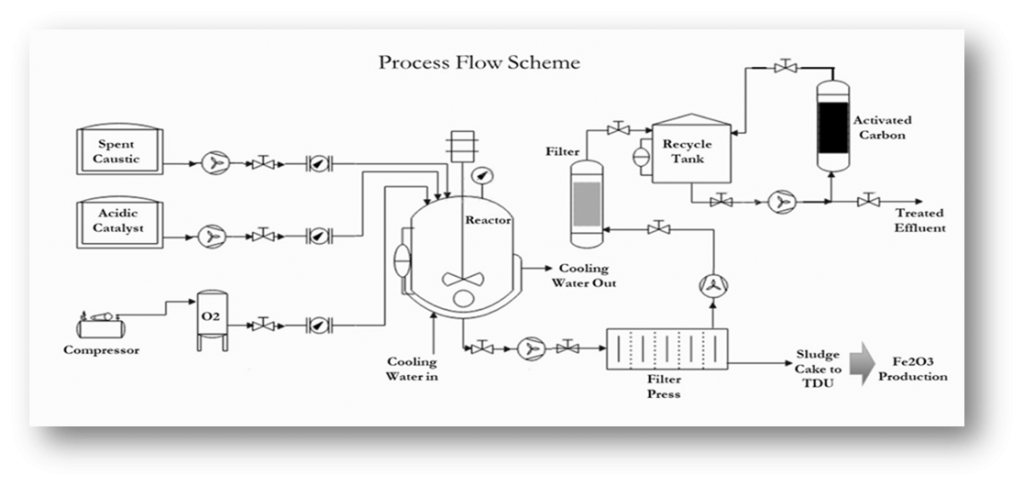
- Can be mobilized
- Can treat COD up to 100,000 mg/l
- COD reduction up to 99.9%
- Sulfides reduced to nil
- pH maintained between 7 to 8
- Fe2O3 secondary product derived from a process
- Easy mobilization, Easy Feeding
- Working under ambient temperature and pressure
- Low power consumption
- Complete dosing system
- Can treat COD up to 100,000 mg/l
- Batch reactor with capacity of 0.5 m3/45 min
- Safe operation
- H2O2 used as the oxidant
- Low maintenance cost
- Easy mobilization, Easy Feeding
- Working under ambient temperature and pressure
- Low power consumption
- Complete dosing system
- Can treat COD up to 100,000 mg/l
- Batch reactor with capacity of 0.5 m3/45 min
- Safe operation
- H2O2 used as the oxidant
- Low maintenance cost